American Plastic Molds are used to produce parts and products in the manufacturing industry. It can be a time-consuming process, especially if your product has complex design features.
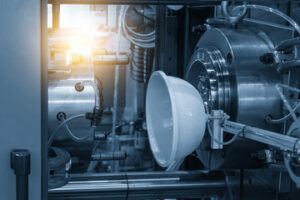
Family injection molds are great for low-volume orders, as they allow you to create multiple parts in one run. This can save you money in terms of materials, production costs and maintenance.
High-temperature injection molding allows plastic manufacturers to produce products with dimensional accuracy and consistency. This is especially important for parts with stringent dimensional tolerances and complex designs. Using this process, molded plastic can also resist high temperatures, making it a great choice for applications in harsh environments. However, there are a few key steps that must be taken into account when producing this type of plastic part.
Optimized Temperature Control
The key to a successful injection molding process involves optimizing numerous parameters. This includes matching the right plastic to its ideal application and ensuring that the mold is heated and cooled evenly. For example, it’s crucial to ensure that the molding temperature remains close to the material’s crystallization temperature. This ensures that the semi-crystalline polymer can fully utilise its unique properties.
Injection Speed
The injection speed of a plastic injection molding machine is an essential factor in the quality of the resulting molded product. A high injection speed allows the molten plastic to enter and fill the mold cavities more quickly, which reduces cycle times. A low injection speed, on the other hand, can result in air pockets or uneven solidification of the molded product. 3. Proper Injection Pressure
While it’s important to maintain a high injection pressure, it is also crucial to keep the injection pressure consistent throughout the entire molding cycle. Incorrect injection pressure can lead to the formation of air bubbles in the molded product, as well as other defects like poor fusion or thermal degradation.
Correctly Incorporating Heat-Transfer Channels
To optimize cooling in a plastic injection molding process, the correct amount of time must be given for the plastic to solidify. This can be achieved by incorporating equidistant channels into the mould design, which will allow all areas of the molded product to cool at an equal rate. It’s also important to remember that the cooling channel diameters must be larger than the injected wall thickness of the molded product.
Injection molding is a versatile and efficient manufacturing process that offers many advantages for plastic producers. By carefully adjusting several parameters, manufacturers can produce high-quality plastic products that meet strict dimensional tolerances and are durable enough to stand up to harsh environments.
Low-Temperature Injection Moulding
The injection molding process involves a polymer being injected into a plastic mold. The injection mold is either a single cavity or multiple cavities, which can form different parts of the same product during one cycle. It is crucial to monitor and control the injection process in order to ensure dimensional accuracy for the final molded product. Injection molding parameters such as temperature, pressure, cooling time and material type are key to producing high-quality molded products.
The barrel (or screw) temperature is essential for ensuring proper melting, mixing and conveying of the plastic. Changing the screw speed or barrel temperature can significantly affect the production rate of the finished product. Injection molding is a very complex process and requires careful balancing of the various parameters to achieve consistent quality.
Depending on the application, the molding composition can contain from 1 to 10 weight percent of reinforcement fibers such as chopped fiberglass of glass, carbon, or polyester and nanometer-sized inorganic fillers like silica. It is also common to add stabilizers to the formulation such as hindered amines, usually at concentrations of from 0.1 to about 2 weight percent.
Cooling time is critical in determining the dimensional accuracy of plastic products. Too short of a cooling time can cause the part to be ejected from the mold too soon, leading to deformation or warping. Too long of a cooling time can reduce the efficiency of the production process by prolonging cycle times. Injection molding temperature and cooling time are both dependent on the specific material used in the formulation.
Dimensional differences in injection molded products can be caused by non-uniform pressure during the injection, packing, cooling and ejection phases of the process. They can also be due to internal stress in the molded products. To minimize these problems, it is important to have a good understanding of the physics of the injection molding process and to optimize all of its parameters.
Cold-Pressure Injection Moulding
Injection molding is a process that involves combining heat and pressure to form the finished plastic product. This is accomplished by injecting a liquid raw material into a closed mold cavity and then applying high-pressure to it until it solidifies into the desired shape. This allows the molded part to be made at a lower temperature than thermosets and can provide a higher yield of parts per hour. However, the balancing of several factors like injection speed, pressure, and temperature settings is essential to ensure quality.
The speed at which the injected material enters the mold is an important variable that impacts everything from the material’s flow performance to the overall finish of the molded product. A well-calibrated injection speed ensures that the melted plastic reaches all areas of the mold cavity evenly and without any defects.
When it comes to selecting the right plastic for your application, you have many different choices. Each resin offers its own unique properties and characteristics, and you need to choose one that’s suitable for the environment in which your product will operate. A popular choice is polycarbonate, which has a high resistance to impact and vibration, as well as UV degradation and chemical corrosion. It also has a high tensile strength and is able to bend to a moderate degree without rupturing.
Once you’ve selected the correct material for your project, it’s time to consider other variables like the cost, durability, and weight of the final product. You also need to think about whether your product will require any inserts or other additional components, and how those will be incorporated into the final molded product.
Lastly, it’s crucial to consider the injection molding cycle time when choosing your plastic. The ideal cycle time is one that provides the highest level of productivity while still ensuring consistent quality. This requires a delicate balance between multiple variables, including the complexity of the molded part design, the materials used, and the injection molding machine’s temperature, pressure, and injection speed settings.
Getting it right the first time is critical to producing high-quality injection molded products. It starts with recognizing the symptoms of common injection molding issues. These include short shots, which indicate incomplete filling, warping, which can occur due to uneven cooling, and flash, or extra material that seeps from the gate of the mold. Regularly monitoring and adjusting injection molding parameters is the best way to ensure optimal results.
Extrusion
Extrusion is a manufacturing process for making long, tube-like shapes or rods. It’s a popular choice for things like drinking straws, curtain tracks, and rods that hold fiber optic cable. It’s also the best method for creating long pieces that have to be manufactured quickly and efficiently.
The process works by feeding plastic granules into an extruder, where the granules are heated and melted into a thick liquid. This liquid is then forced through a die, which takes on the shape of the final product. The extruded product is then cooled down and solidified. Extrusion can also create sheets and films from plastic that are very thin, which is important for applications like windshield wiper blades or vinyl signs.
While extrusion is a great manufacturing option for long, continuous products, it’s not as good at producing 3-dimensional parts. It can also be challenging to make very intricate surface details with this process. However, the benefits of extrusion can outweigh its limitations for many projects.
When it comes to choosing a production method for your plastic part, there are many considerations to take into account. The type of project you’re working on, the required quality, and your budget are just a few factors to think about. You may also need to consider whether a particular manufacturing process will be suitable for your production environment and the materials you’re using.
The injection molding process is well-known for its versatility and engineering precision. It combines engineering accuracy, material science, and design flexibility to achieve superior results. The liquified plastic is injected into a mold that’s shaped to match the desired product. The molded plastic is then cooled and solidified before it’s ejected from the mold.
The extrusion process is similar to injection molding in that the liquified plastic melts and takes on the shape of the dye. But that’s where the similarities end. In extrusion, the plastic is pushed through a die to form a long, tube-like shape or rod. After it’s cooled down and solidified, the resulting product is cut to length to complete the project.